Whether you live in a high-rise or suburban home, there’s no reason to settle for traditional tiles or shingles. A metal roof provides superior protection while adding modern appeal to your property.
Avoid the cheapest felt underlayment, which will soak into attics, insulation, and framing. Instead, invest in a moisture-resistant synthetic underlayment. Contact Metal Roofing Erie PA now!
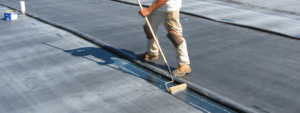
Metal roofing costs more than shingles upfront but lasts for decades, saving homeowners money on home maintenance and repair expenses and homeowner’s insurance premiums. Metal roofs typically have a reflective solar coating, which reduces heat buildup and lowers air conditioning costs. They’re also much quieter than shingle roofs, helping to reduce noise in the house. In addition, they are usually easier to install and can be placed on top of existing shingles.
The longevity of metal roofing depends on several factors, including the material used and local climate conditions. Copper, zinc, and aluminum roofs last the longest and require very little maintenance. They’re highly durable and can withstand high winds, snow, and corrosive environments. They’re also environmentally friendly and fully recyclable. However, they may be more expensive than other metal roof types and are prone to denting. They can also be susceptible to oil canning, a wavy or rippling appearance that occurs in flat areas of the roof panels due to thermal expansion.
Steel roofs can last up to 60 years and are less costly than some other metal roofing options. They’re durable and resistant to corrosion, but they’re also more prone to dents than other metal roofs and can be difficult to match in color. Like other metal roofs, they can suffer from damage caused by fallen tree branches or hailstorms and need to be inspected regularly for any signs of wear. They’re also susceptible to thermal expansion and contraction, which can cause a wavy or rippling effect known as oil canning.
The pitch, or slope, of the roof also influences longevity. A steeper roof’s surface sheds water more effectively, reducing the risk of pooling and other moisture-related issues. Regular inspections and cleaning can help extend a metal roof’s lifespan, and using protective coatings can make it more resistant to moisture, corrosion, and harmful UV rays. Choosing a metal roof with a Class A fire rating also helps to ensure safety during lightning strikes.
Durability
The upfront cost of metal roofing may be more than traditional shingle options, but these roofs last for decades and reduce the need for frequent repairs or replacement. They also save homeowners money in the long run on energy costs.
Many types of metal roofing can withstand harsh weather conditions, including high winds, heavy snowfall, and hailstorms. However, specific factors like climate and installation techniques determine a metal roof’s longevity. If you live in a location with harsh weather, consider using a thicker gauge metal or opting for a standing seam roof that offers greater durability.
Corrugated and sheet metal roofing can rust if not properly maintained, but coatings that resist corrosion, like Kynar, significantly lengthen the life of the roof. Additionally, regular inspections of the roof and removal of debris can prevent moisture damage and help maintain a clean appearance.
Most experts agree that you should have your roof inspected at least once a year, and this is particularly important with metal roofing. In fact, a professional inspector can spot potential problems that you might not be able to see yourself and recommend the best course of action to avoid serious issues.
One of the most common causes of premature failure in metal roofs is loose fasteners, which can allow water to penetrate the roof and lead to structural damage, leaks, mold or mildew growth, and other interior problems. During an inspection, your roofer will check all fasteners and sealants to ensure they’re intact.
A premium metal roof, such as copper or stainless steel, can last for 75 years or more. These metals are naturally ductile and durable, and their beauty adds to the curb appeal of any home. They’re also highly regarded for their fire-resistant properties and are often used to accent other roofing materials.
For example, a copper roof adds visual interest to a shingle or tile roof and can be used for flashing, gutters, chimney caps, bay windows, and cupolas. Stainless steel is also used as a metal roofing material due to its durability and corrosion resistance, which makes it an excellent choice for residential homes that require a long-lasting and attractive roof.
Energy Efficiency
While metal roofs aren’t new, they are continuing to grow in popularity as more homeowners realize the many energy-related benefits they offer. The ability to reflect the sun’s UV and infrared rays, cool the surface quickly, and provide more efficient temperature regulation inside the home all help lower cooling costs and the overall energy used by the house.
Unlike traditional shingle roofs, metal roofs are able to reflect up to 70% of the sun’s heat and sunlight. They can significantly cut the average homeowner’s energy bills, especially in warm climates. A well-ventilated metal roof can also save money on cooling energy by allowing hot air to escape and promoting the flow of cooler air.
This thermal performance is largely due to a combination of the roof’s reflectance and emissivity characteristics. Both measures of a roofing material’s ability to radiate heat are important for improving a roof’s energy efficiency, and can be evaluated using a solar reflectance index (SRI) test. A roofing system’s SRI rating is based on its ability to reflect the sun’s rays and absorb infrared rays, with a higher score indicating a more reflective roof.
SRI tests can also reveal a metal roof’s ability to emissively release the absorbed heat, or its thermal emittance. A roof’s thermal emittance is based on the percentage of the reflected and emissive characteristics of the roofing materials, along with any additional layers that are added to the structure. A roof’s thermal emittance can be improved by adding insulation and increasing the thickness of the metal roofing.
Another important factor in a metal roof’s energy efficiency is the type of steel it is made from. While there are a number of steel options that can be used in roofing, stainless steel is preferred for its corrosion resistance and durability. A high-quality stainless steel product is designed to last 50 years or more, and requires no maintenance beyond occasional washing with water and a mild detergent.
Although metal roofs require much less maintenance than shingle roofs, they still need regular inspection and care. The best way to protect the investment is to hire a reputable contractor, perform routine maintenance tasks and address any issues as soon as they arise.
Low Maintenance
Metal roofing can last 50 years or more with minimal maintenance or repairs. It also has a wide range of colors and finishes to suit any style, and it is fire resistant and energy efficient. In addition, it can withstand most weather conditions, including hail and heavy winds. However, it is important to select a quality installer and ensure that your roof is properly maintained.
The lifespan of a metal roof depends on the type and thickness of the material, as well as environmental factors. Copper, steel, and zinc are all excellent choices for a long-lasting roof. They are available in a variety of styles and colors, and they can be installed with or without a protective surface coating.
Regular cleaning and inspection can keep metal roofing in top condition. In addition, it is important to use non-cracking sealants on any joints or seams in the roof to prevent water from seeping in. These products are typically inexpensive, and they can be applied easily. Inspecting for rust or corrosion is another important part of regular roof maintenance, and these areas can be repaired quickly to keep the metal in good shape.
A metal roof is more durable than shingles and can withstand damage from falling debris. However, it is still possible for the roof to develop dents or lose its paint finish due to extreme weather conditions. A good roof contractor can advise homeowners on how to protect the metal roof and minimize damage from debris.
Metal roofs are often built to withstand wind gusts of up to 140 miles per hour. While this can result in a slight reduction of the roof’s lifespan, it can help to reduce the amount of maintenance needed.
In addition, a metal roof is not as noisy as a shingle roof when it rains. However, noise can be a problem for some people. An experienced roofer can add proper underlayment and insulation to reduce noise levels.
Although metal roofs require less maintenance than other roofing materials, they should be inspected annually to ensure that all flashing and seams are secure. Failing to do this can lead to roof leaks, so it is crucial to hire a professional roofing contractor to perform this maintenance.